Its appetite for coal makes Big Steel a big polluter. A startup is moving to help industry kick its habit with an electrifying technology.
China’s industrial heartland, Japan’s coastal manufacturing hubs, and even some cities in America’s ravaged Rust Belt are humming with the low roar of mills forging steel, the most widely used metal in the world but also one of the dirtiest to produce.
Blast furnaces tower more than 100 feet high, their bowels heated to blinding-white temperatures that melt iron ore in midair before it pools at the hearth. Metallurgical-grade coal, known as coke, separates the metal from its ore, and limestone strips it of impurities that are skimmed off the top and dumped as glass-like slag. The molten stream of resulting pig iron is tapped from the furnace bottom and carted off in massive ladles to yet another oven that turns the iron into liquid steel.
The furnaces never sleep, tirelessly pumping out steel to manufacture everything from sewing needles and washing machines to bridges and cargo ships. And while the Iron Age-old process has seen some technological updates in the last 150 years, the underlying chemical equations have stayed much the same. As always, they rule: Large amounts of carbon dioxide must be emitted when making steel.
Boston Metal is hard at work to overhaul that dictum. Based seven miles north of Boston in Woburn, MA, the startup is commercializing Molten Oxide Electrolysis (MOE) as a way to make steel with zero emissions. The company’s technology uses electricity to separate iron from its ore, doing away with the carbon dioxide-heavy processing steps that involve coke, limestone, and blast furnaces. If electricity is sourced from renewables, steel from the vaults of Boston Metal won’t leave any carbon footprint.
Chairman and CEO Tadeu Carneiro said the company is “ushering in a new era of metallurgy” to relieve the steel sector of its centuries-long appetite for coke that today makes it the largest industrial consumer of coal.
The Organisation of Economic Co-operation and Development and the International Energy Agency see Boston Metal’s process as a serious contender to cut carbon emissions in the long run. Both place it halfway up the Technology Readiness Level scale, developed by NASA and widely used by government agencies and research institutions to judge how far along a given technology is on its way to market.
The American Iron and Steel Institute, a prominent trade association, financed the early development stages of MOE and has since kept in touch with Boston Metal’s progress. The institute’s take is that “reducing greenhouse gas emissions in the steel industry may require deploying multiple technologies, and MOE is a possible tool to reach this goal.”
The workhorse of Boston Metal’s innovation is its reactor: a ceramic electrochemical cell shaped like a drum that holds a liquid soup of oxides at 1,600 degrees Celsius. Iron ore dissolves into the soup as soon as it hits the surface. An electric current travelling between terminals at the bottom and top of the cell then decomposes the iron ore, producing the desired liquid iron and pure oxygen as the only byproduct.
By comparison, traditional steelworks on average emit almost 2 tons of carbon dioxide for every ton of steel they produce. More than 2 billion tons of steel were cast in 2020 — a 10-fold increase since 1950 that is nowhere near leveling out — accounting for at least 7 percent of total greenhouse gas emissions worldwide.
“If steel were a country it would be the third largest CO2 emitter,” said Donald Sadoway, professor of materials chemistry at the Massachusetts Institute of Technology. Sadoway invented the particular MOE setup used by Boston Metals and co-founded the company in 2012. “Number one is China, number two is the US, and number three is the Republic of Steel.”
Most emissions escape the blast furnace as it extracts the iron from its ore, but a number of ancillary facilities also emit carbon dioxide or other hazardous discharge. Those include coke ovens to purify coal, pelletizers and sintering machines to pretreat the iron ore, crushers to ready the limestone, and basic oxygen furnaces to purify the pig iron. All or most of them would be made obsolete in an MOE-based steelworks that has electrified its operations.
The simplicity of the process would also keep capital expenditure and operating costs down. “If you want to increase capacity with a blast furnace, it really has to be a 10,000-cubic-meter blast furnace and all of the stuff that goes with it,” Sadoway explained. “That step is too high. MOE allows you to grow in a way that the step size is that of a staircase instead of that of a cliff.”
Capital costs of a newly erected steel plant would drop from an estimated $4 billion to somewhere in the millions. Because the electrochemical cells are modular, steel output could be adjusted by stringing several cells together in rows upon rows, similar to the practice in aluminum smelters that also use a form of electrolysis, although at lower temperatures. The cells would use energy 20 percent more efficiently because they control the iron-yielding reaction more tightly than a blast furnace, which, true to its name, acts like an explosion, radiating heat in all directions.
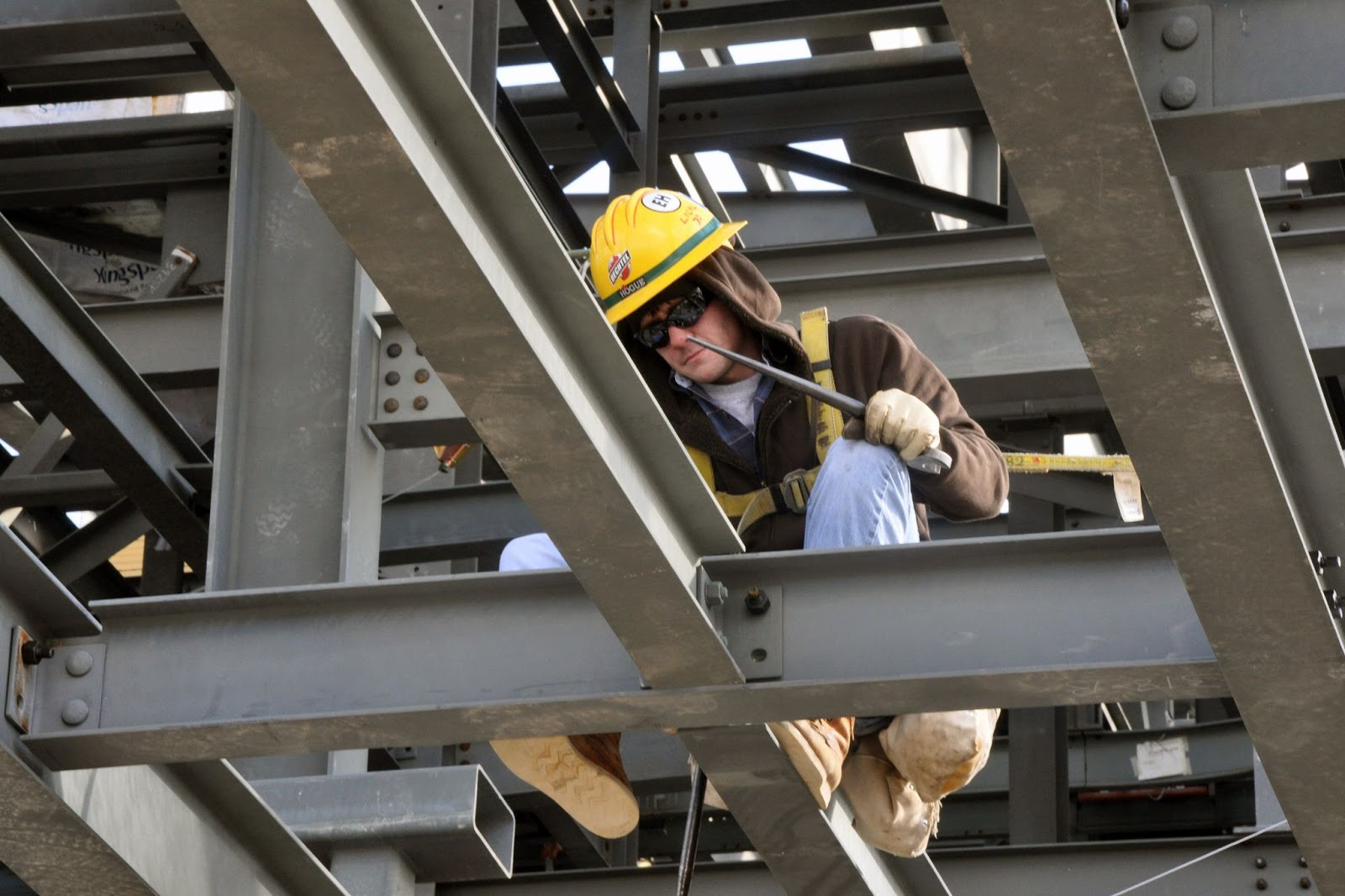
To commercialize its technology, Boston Metal is scaling its cells to semi-industrial output. In 2015 the company built a cell running currents at 10,000 amperes, capable of churning out enough iron for 600 tons of steel per year. Another, larger cell more than doubled that capacity. The goal for 2022 is a cell producing 3,000 tons of iron per year. “At that point,” Sadoway hopes, “people will say, ‘We’re convinced that this thing is scalable.’”
Several companies are financing the scale-up. Last March, Boston Metal exceeded its goal of raising $50 million in its second round of funding, bringing its total to well over $100 million. The German carmaker BMW is the latest investor to jump on board, joining prominent clean-tech supporters such as the Bill Gates-backed Breakthrough Energy Ventures as well as big mining companies including Australia’s BHP and Brazil’s Vale.
“Our investors span across the steel value chain,” said Carneiro, “from the upstream mining and iron ore companies to the downstream-end customer, and validate Boston Metal’s innovative process to produce high-quality steel, cost competitively and at scale.”
Support for Molten Oxide Electrolysis to produce steel wasn’t as vocal when Boston Metal began life in Sadoway’s laboratory at MIT. “I was ready to do this back in 1988. But no one believed this stuff,” Sadoway said. “Back in the ‘80s, people viewed electricity as a very refined form of energy. You wouldn’t dare use electricity to make something as mundane as steel.”
“And the environmental imperative wasn’t there,” he added. “In the 1980s the notion that CO2 emissions was something that we should be abating, that wasn’t there.”
Without the pressures of the climate crisis, steel producers had little incentive to uproot their machinery and change their emission-heavy ways. “With these massive, high-tonnage industries there comes a risk aversion,” said Sadoway. “This is all capital intensive. Building a [new] steelworks today would probably cost you 4 billion dollars. These things have lifetimes of 30 to 40 years. So these people aren’t about to go jumping to look for something else.”
Sadoway, on the other hand, came into the steel business as somewhat of an outsider. He had long focused on teaching and research and only recently turned his attention to entrepreneurship when his students urged him not to consign his innovations to the laboratory, where they would likely have little impact on society.
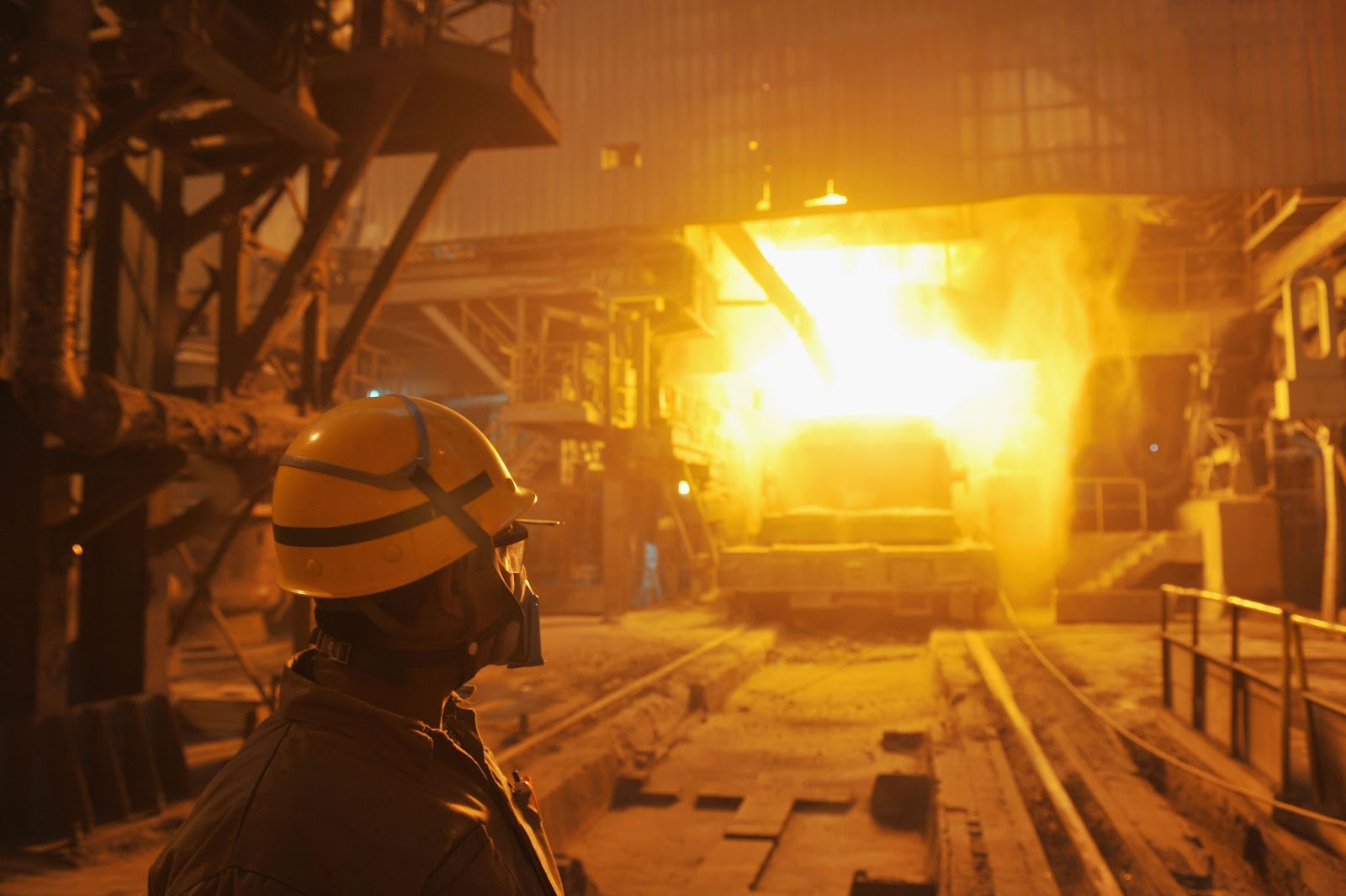
His inspiration to rethink steel came from his interest in another metal’s emission problem, that of aluminum, the second-most-produced metal behind steel. Aluminum smelters, like Sadoway’s MOE cells, are electrolytic, but they emit substantial amounts of carbon dioxide. The crux of aluminum’s problem is the electrochemical cell’s anode, one of the terminals that pumps the electric current through the cell. Because the anode is carbon-based, it breaks down into carbon dioxide over time.
A project with NASA, finding a way to make oxygen on the moon from nothing but lunar dirt, offered a way for Sadoway and his team at MIT to test key ingredients of what was to become Boston Metal’s MOE. Using an anode made of precious metals — exotics like platinum and iridium — and passing current through a cell the size of a coffee mug, the team smelted its first batch of iron ore. But the anode was too expensive for anyone besides NASA.
“I knew that if I wanted to have something that would work on planet Earth we would have to have a practical anode,” said Sadoway.
The breakthrough came in 2011, when Sadoway and colleagues discovered the holy grail: an anode made of chromium alloy that was chemically inert and affordable at scale. “At that point we knew we had all the elements to make tonnage steel and do so in a way that’s cost competitive,” Sadoway recalled. “We can’t build tonnage steelworks out of iridium platinum. If you have to buy your electrodes at Tiffany’s you’re in trouble. So that was really big.”
From there on, Sadoway’s team didn’t limit itself to purifying just iron for the sake of steel. Testing the versatility of their setup, they targeted metal after metal to see which ones would readily separate from their ores. “We just hopscotched around the periodic table, just kept checking, checking, checking,” said Sadoway. “You give me dirt, I’ll turn dirt into metal.”
The results were stunning. Apart from iron, Boston Metal’s cells can also purify nickel and chromium, which together with iron are the ingredients for stainless steel. Titanium, as strong as steel but only half its weight, is another possibility, as well as zirconium, used for biomedical applications such as dental implants and prosthetics. Beryllium, used for gears in the aerospace industry, and rare earth metals for electronics are also on MOE’s extensive menu — all free of carbon emissions.
“MOE is not only the way to make carbon-free steel, but it’s a platform technology and it could cut a swathe across all of metallurgy,” said Sadoway.
With scale-up operations having started last month, Boston Metal is well on its way to disrupting the industry. Although the company is not explicit about where its technology would be deployed first, any viable area would need to supply ample amounts of clean electricity. Hydroelectric power — renewable, nonintermittent, and cheap enough to compete against fossil fuels — would be a prime source within the US, in Sadoway’s native Canada, or in Carneiro’s native Brazil.
“I think it’s going to be a case of: Let’s look at where the most favorable conditions are for the first plant,” Sadoway said. “Let’s worry how to scale under those circumstances, and then we can start to look at other places, maybe places that predominantly use solar.”
Until that point, legacy steel producers still have time to prepare. Boston Metal expects its process to be fully commercial on an industrial scale by 2025. The company sees electrochemical cells gradually replacing existing equipment phased out at the end of its life. “I don’t want people to think that I’m telling the steel legacy producers to take the wrecking ball to their existing equipment,” said Sadoway.
Established industry giants recognize the demands of global climate goals and are pursuing their own greening projects to shrink their carbon footprint or eliminate it entirely. SSAB and ArcelorMittal in Sweden, Voestalpine in Austria, Thyssenkrupp in Germany, and Baowu in China are all investigating hydrogen as a substitute for coke in their blast furnaces, which would then emit steam instead of carbon dioxide. As with Boston Metal’s electrolysis, hydrogen technology is in the process of scaling up.
“There could be a plurality of carbon-free approaches,” Sadoway speculated. “People may say if we want a small plant, hydrogen makes sense; if we want bigger tonnage, then MOE makes sense. I don’t know. But I think it’s exciting to see that people are really starting to look at alternatives. And at some point, the legacy producers may be drawn in.”
Related front page panorama photo credit: Designed by Mathilde Fallot /WhoWhatWhy, Jesper Schoen / wikipedia (CC by 2.5)